At Kingsmill, we always recommend process of exothermic welding to join copper conductors together in an earthing system…let’s explain.
A proper earthing system uses materials that provide:
- A low resistivity path to earth (or ground),
- the capacity to carry high currents,
- excellent corrosion resistance,
- and mechanical strength.
Why is it so important that the connections in your earthing system maintain the above criteria? It’s simple. Let’s take a look at the exothermic welding process and understand how it works.
Exothermic welding is an aluminothermic (chemical) reaction that takes place between an aluminium powder and a metal oxide, or in the case of your copper earthing system, a copper oxide. The aluminium powder reduces the copper oxide and in the process, it produces a huge amount of heat.
As a reaction, it is defined as 3Cu₂0 + 2Al → Cu + Al₂O₃, but put more simply, an exothermic reaction results in the production of molten, super-heated copper and an aluminium oxide slag.
So, you might ask, how does this contribute to a good earth connection?
To answer that question, it’s good to know the basic welding procedure.
We supply our Kingsweld Exothermic Weld Metals in pre-measured doses that are ready for use in the construction of your earthing system. They are packed in plastic cartridges, that each have two compartments, one (the largest) containing the copper oxide, and the second, the smaller compartment, that contains the finely ground aluminium powder.
As the reaction produces a molten metal, a mould is used to contain the reaction and channel the molten metal to the conductors being joined. We manufacture our moulds from a high-density graphite that allows for the machining of precise cavity dimensions and detail.
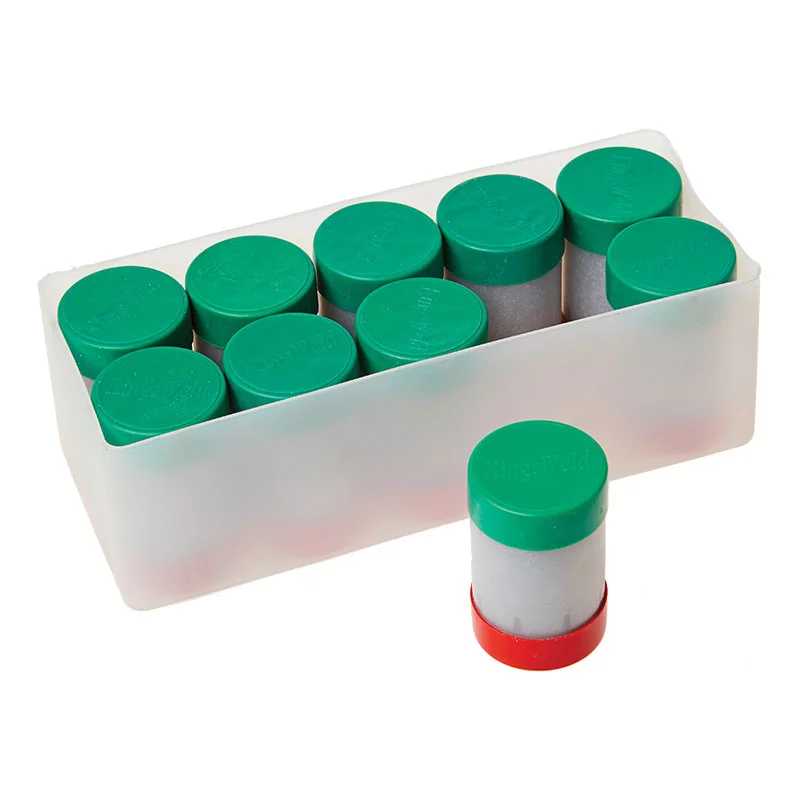
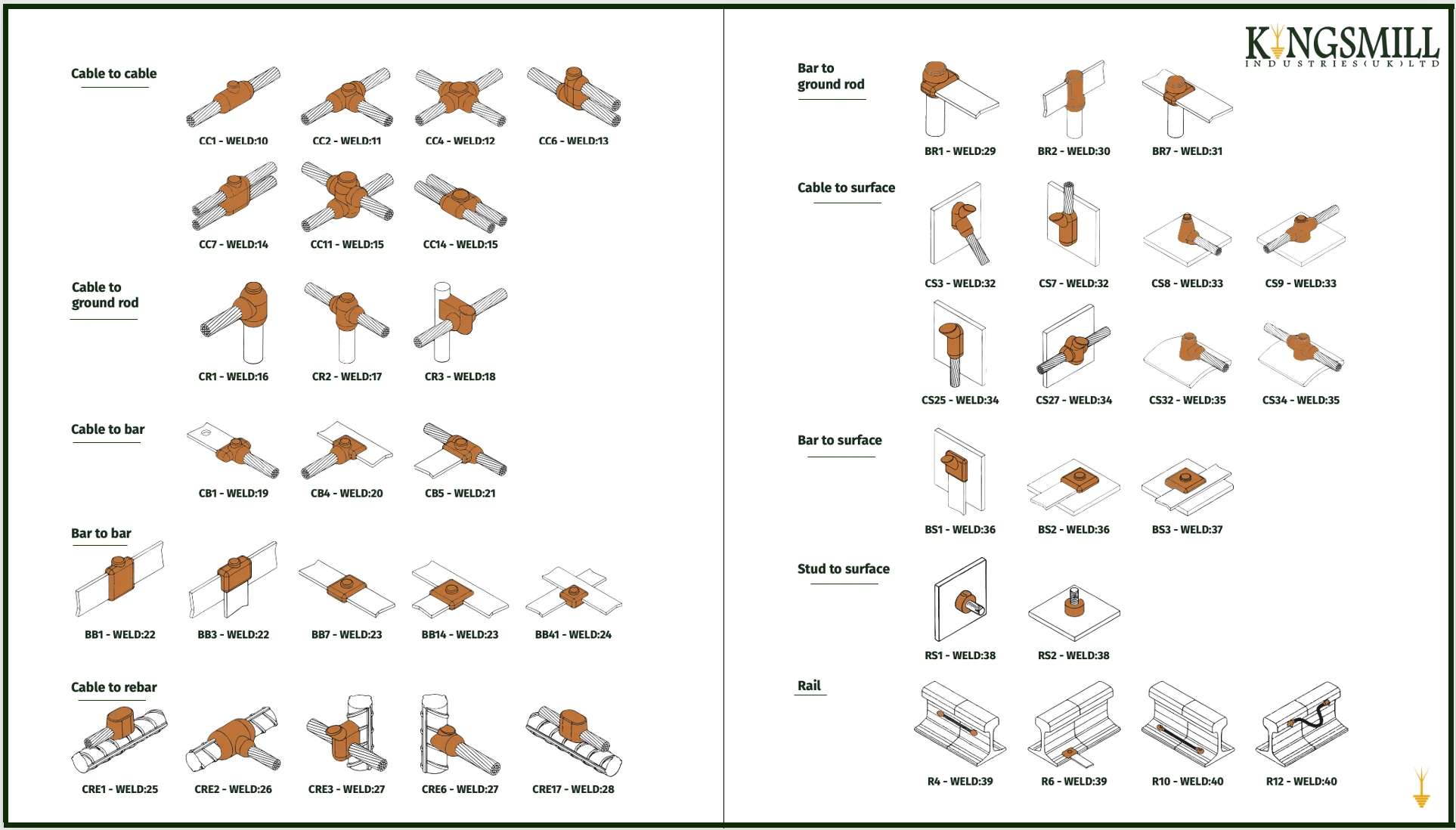
Now, if you had a minute to take a look at our selection charts, you might wonder why there are tens of different sizes of weld metals. We size our weld metals according to the weight of the main weld metal (or copper oxide) – 15g through to 250g. Of course, some of our larger conductor configurations require more than one metal. Earlier, we learned that the exothermic reaction produces a huge amount of heat, in-fact up to 2000°C. This heat, and the molten metal it produces, is what makes this product so exciting to use in your earth system. Remember, that our aim is to partially melt copper conductors to create a welded, permanent joint. Those copper conductors are not preheated, but are at ambient temperature, and the melting point of copper is about 1085°C!So here’s the secret! The weld metal that you use, is sized according to how much heat will be required to partially melt the size of the conductors that you are using to form a welded joint.Think of it this way – You need to melt something very quickly and to do so, you are introducing it to a slug of super-heated, molten metal. The time from start to finish is seconds, and within this time, the reaction that started from the molten metal is formed and the joint is officially created. Hence the reason, that slug of metal needs to be of sufficient heat and size to create the joint that you require. Now back to the exothermic welding process…
Once you have the proper tools, follow the steps below:
- Clean the conductors using a wire brush and then place them into the graphite mould weld cavity, making sure to keep a 3mm gap between them. Then, close and lock the mould tight using the appropriate handle clamp for that mould size.
- Now, place a thin metal retaining disc over the top of the “tap hole”. This helps prevent the dry weld metal powder from entering the weld cavity and allows the exothermic reaction to take place within the reaction chamber / crucible.
- Then, pour the contents of the main (large) weld metal compartment, (the copper oxide) into the crucible.
- After doing so, sprinkle the contents, the aluminium flake, into the smaller compartment on top of the copper oxide – Do not mix them!
- Now, just like every love story, there is always a spark. So in order to start the reaction, we create a spark from a simple flint ignitor. The aluminium powder also known as the “starter powder” is available when you purchase our weld metals, and is easily ignited with a temperature of 450° The spark from a simple flint ignitor provides that temperature, and voila, the chain reaction starts!
- Last but certainly not least, after approximately 20 seconds or so, you can open the mould with the handle clamp, and see your beautifully created KingsWeld mould.
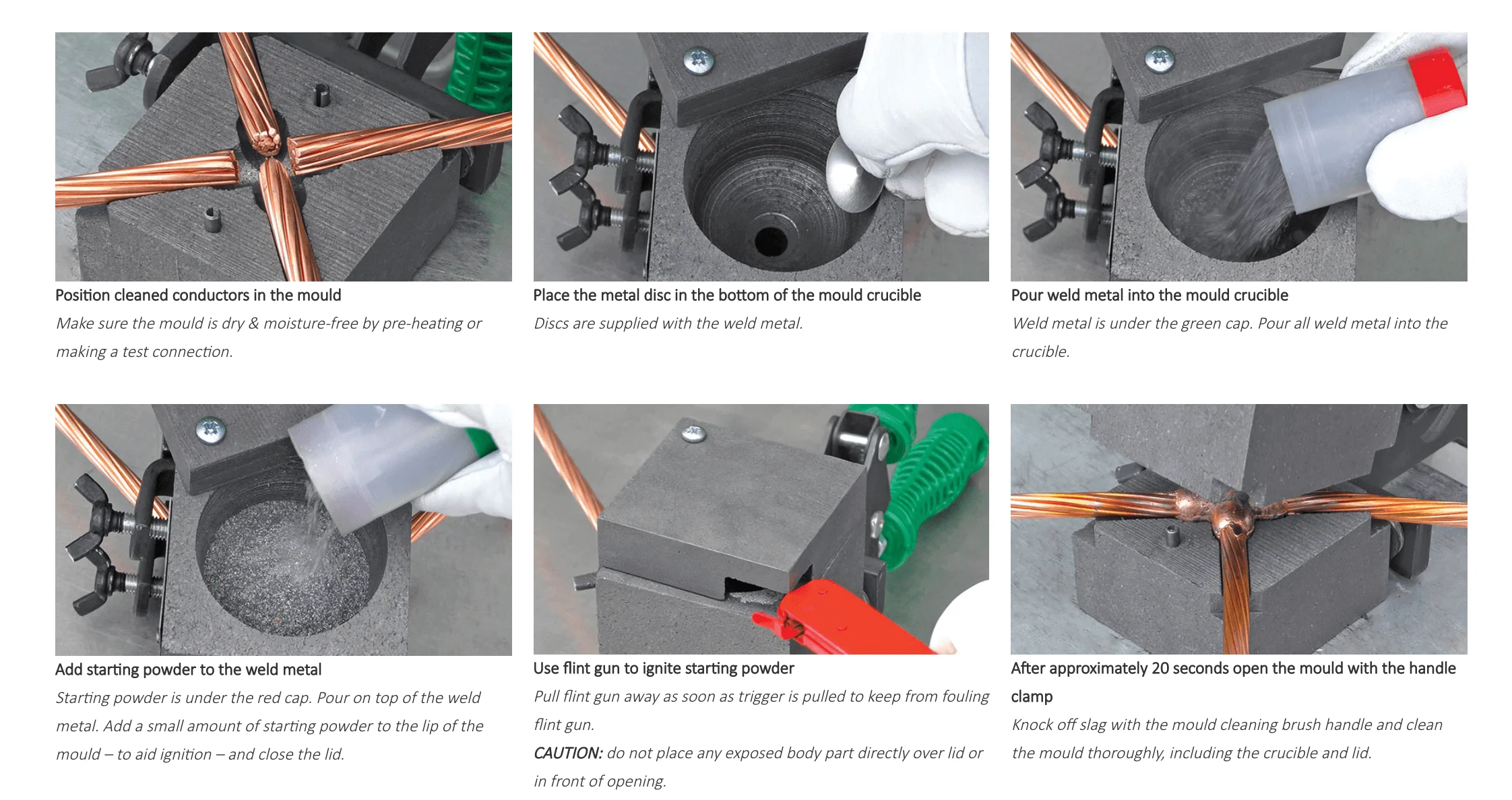
If you recall the equation above, the copper oxide is now molten copper, and the aluminium powder is an aluminium oxide slag. You see what happens, is that the molten copper melts the thin steel retaining disc and flows freely into the weld cavity, melting the copper conductors therein and forming the aluminium slag. This newly formed aluminium slag stays in the reaction chamber/crucible and is easily removed, once the graphite mould has cooled.
Good news, we all love that, especially these days, is let’s say you need to make more moulds. Well, our graphite moulds can last up to fifty or sixty even connections, of course that is if you take good care of them. Check out the instructions on how to do that here.
Caveat emptor – as with any exothermic welding process, it is important that you follow our instructions and use the correct PPE (Personal Protective Equipment) to safeguard both yourself and your colleagues.
A good friend once told to me that, “Anyone can make an exothermic weld metal, but only a few can make it consistently and in high volume to meet market demand” – those words are so true!
There is more to manufacturing and supplying exothermic welding than meets the eye! That is why, it is crucial to use products produced by a reputable manufacturer … like ourselves, Kingsmill Industries.
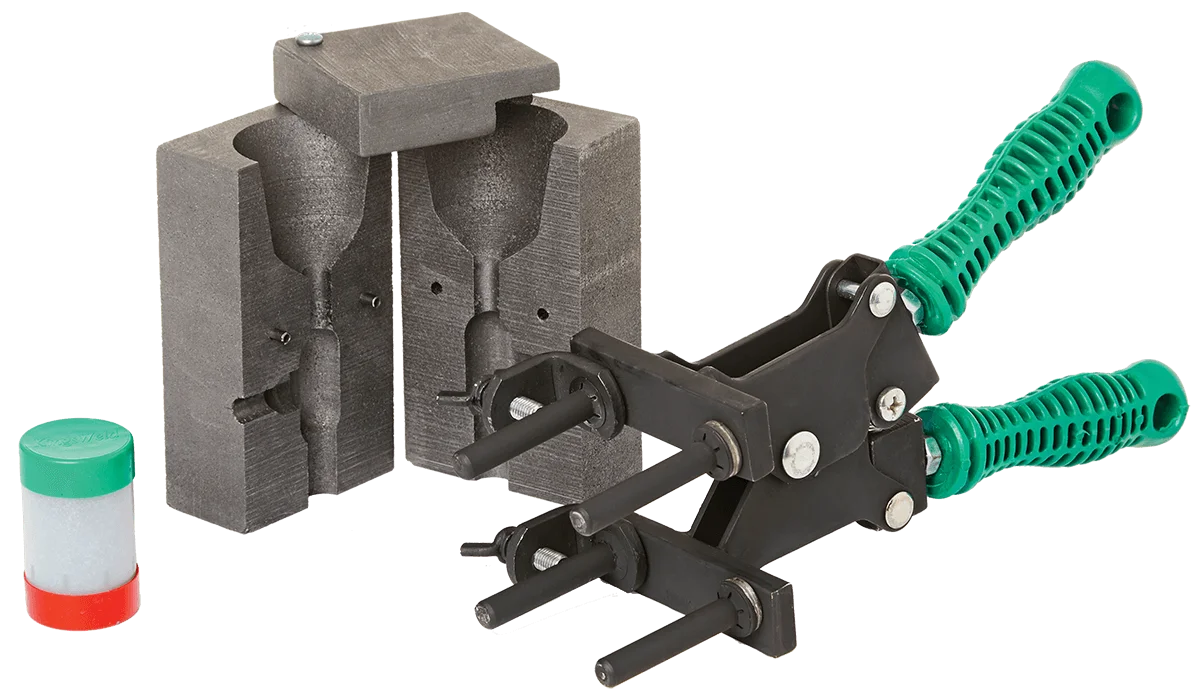
- The current carrying capacity of the connection is greater or equal to that of the conductor itself. (This is because it is a weld formed with at least 97% copper content).
- Because it is a weld – it has a lower electrical resistance than a mechanical connection. Neither does it loosen with time or allow corrosion to build up inside the joint itself (thus increasing impedance).
- The weld does not deteriorate with age. It has exceptional corrosion resistance due to its very high copper content (97%+)
- The weld takes place at some 2000°C thus forming a molecular bond – note – mechanical connections, whether bolted or crimped, do not form a molecular bond!
- Our Kingsweld exothermic weld can withstand repeated current surges without deterioration!
- Our process does not require external power on site, and it is easy for your operatives to use.